Company Name | Contact Info | Location | ||||||||||||
---|---|---|---|---|---|---|---|---|---|---|---|---|---|---|
BAROMAK MAKİNE SAN.TİC. LTD. ŞTİ.
Çalı Sanayi Bölgesi 37. Sokak No: 23/B / Nilüfer / BURSA / TÜRKİYE
|
Contact Info: +90 539 843 47
|
Hall: E
Stand: E5.14
|
||||||||||||
Product Groups | ||||||||||||||
|
- Company Info
- Products
- Represented Companies
- Company Brands
Baromak, a company manufacturing brush sanding machines, spray painting machines, calibration machines, and drying lines for the wood processing sector, may appear relatively young in this field, but with its experienced team of experts boasting 15 years of experience in the wood processing industry, both domestically and internationally, it has gained significant expertise and a portfolio. Operating in production facilities located in Bursa Çalı Industrial Zone, our company prioritizes customer satisfaction and continues its machine production without compromising on quality. In a short period, our aim is to become a prominent figure in the field of sanding machines in Turkey and worldwide. Committed to environmental sensitivity, our company generates its own electricity with a solar energy field (GES) built on the factory roof. Additionally, we collaborate with city management for greening the operating environment and waste disposal. Our company can meet the needs of small, medium, and large furniture companies.
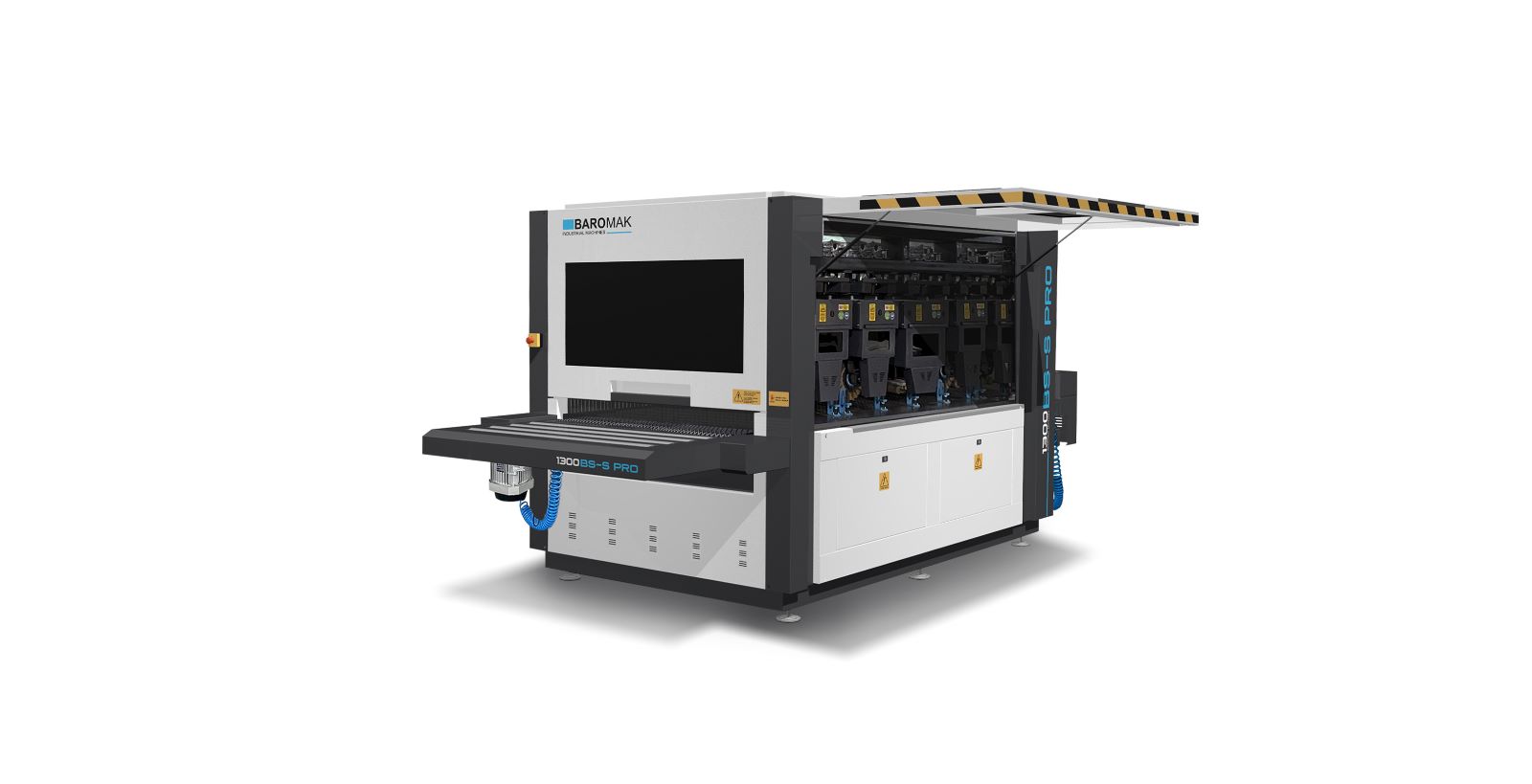
- 6 stations, fully oscillating, working in both directions - Possibility to make coarse and primer sanding separately with all stations - Sensitive with 0.1 mm precision via touch screen at each station possibility of printing. - Memory feature - Opportunity to receive service and training with remote connection - Strong body and stylish design - Schneider brand electrical equipment - Hermes brand double sided sanders - Polyamide antistatic brushes - Very easy sandpaper changestation structure - Stations with drawers attached to the ceiling - Automatic lubrication system - Built-in conveyor - Standard Side Sanding Station
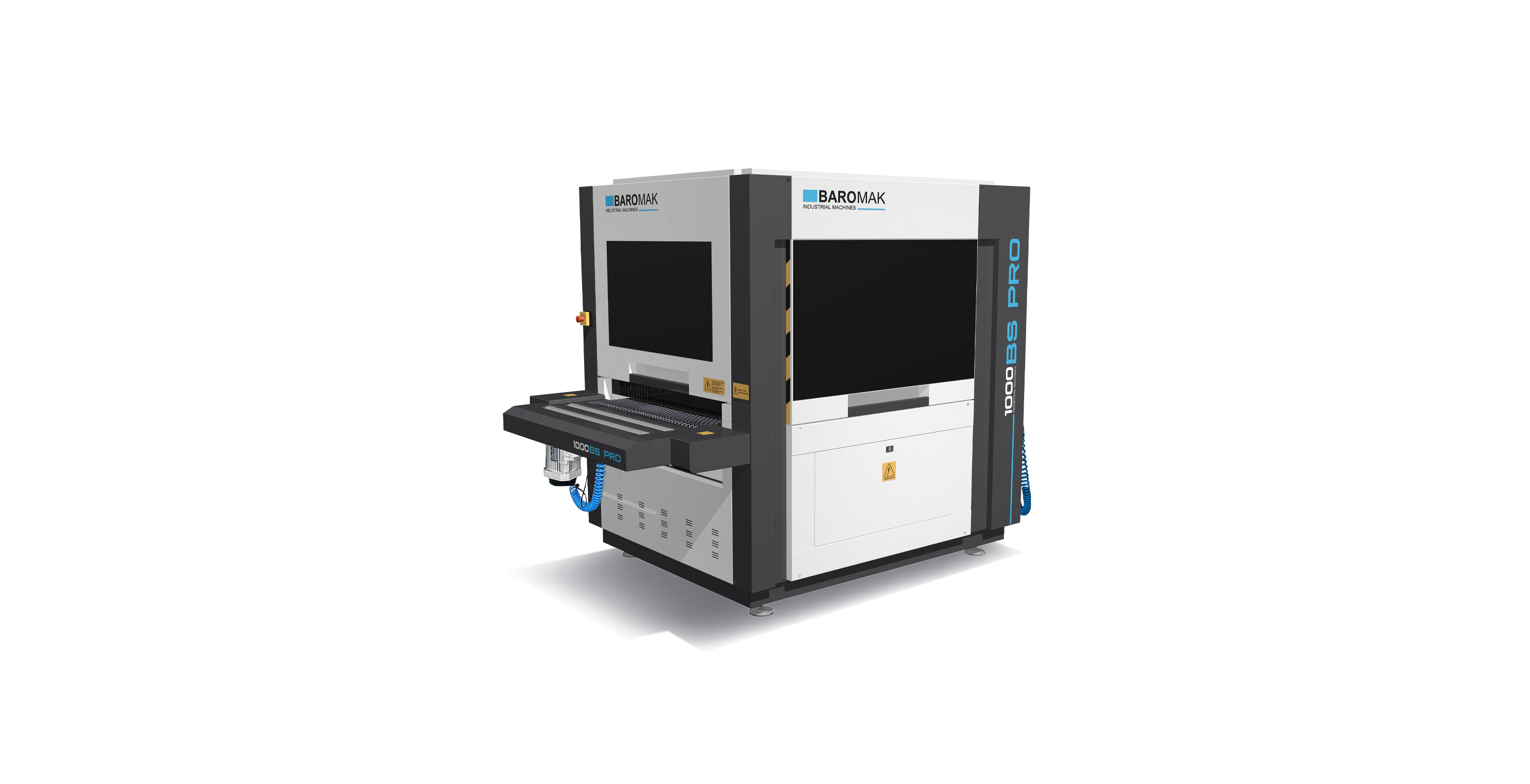
- 4 stations, fully oscillating, working in both directions - Possibility to make coarse and primer sanding separately with all stations - Sensitive with 0.1 mm precision via touch screen at each station possibility of printing. - Memory feature - Compact body and stylish design - Schneider brand electrical equipment - Hermes brand double sided sanders - Polyamide antistatic brushes - Very easy sandpaper changestation structure - Stations with drawers attached to the ceiling - Built-in conveyor
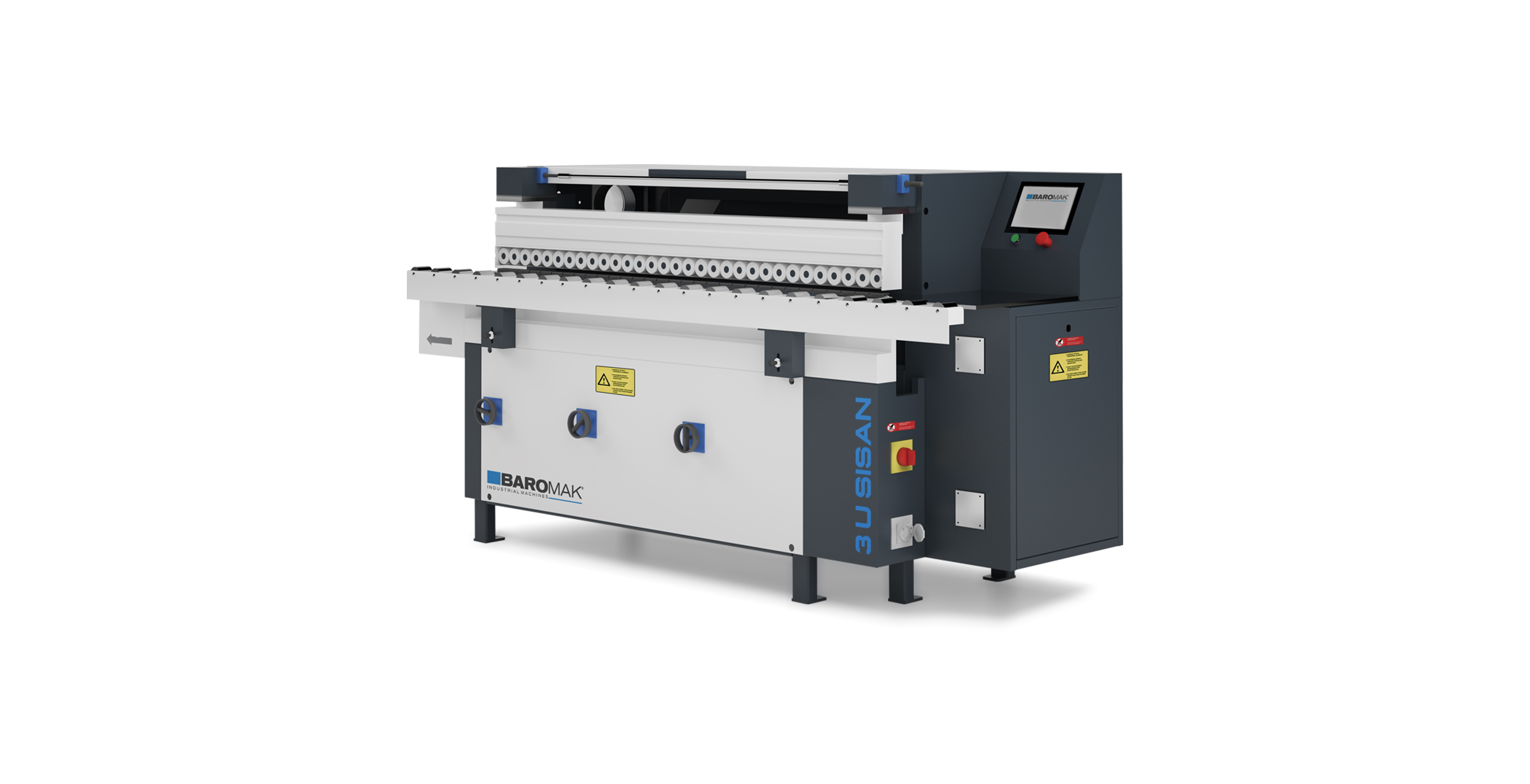
-Easy to use with conveyor pressure system that can be automatically adjusted according to product thickness. -There are 3 stations: 1 disc sander and 2 bay window sanders, which can be adjusted independently of each other. -For a better surface quality, there is oscillation at each station and the oscillation is done by an independent motor. -Easy to use with 10 inch touch screen and user-friendly interface. -It provides superior performance in side sanding thanks to its automatic speed adjustable conveyor.
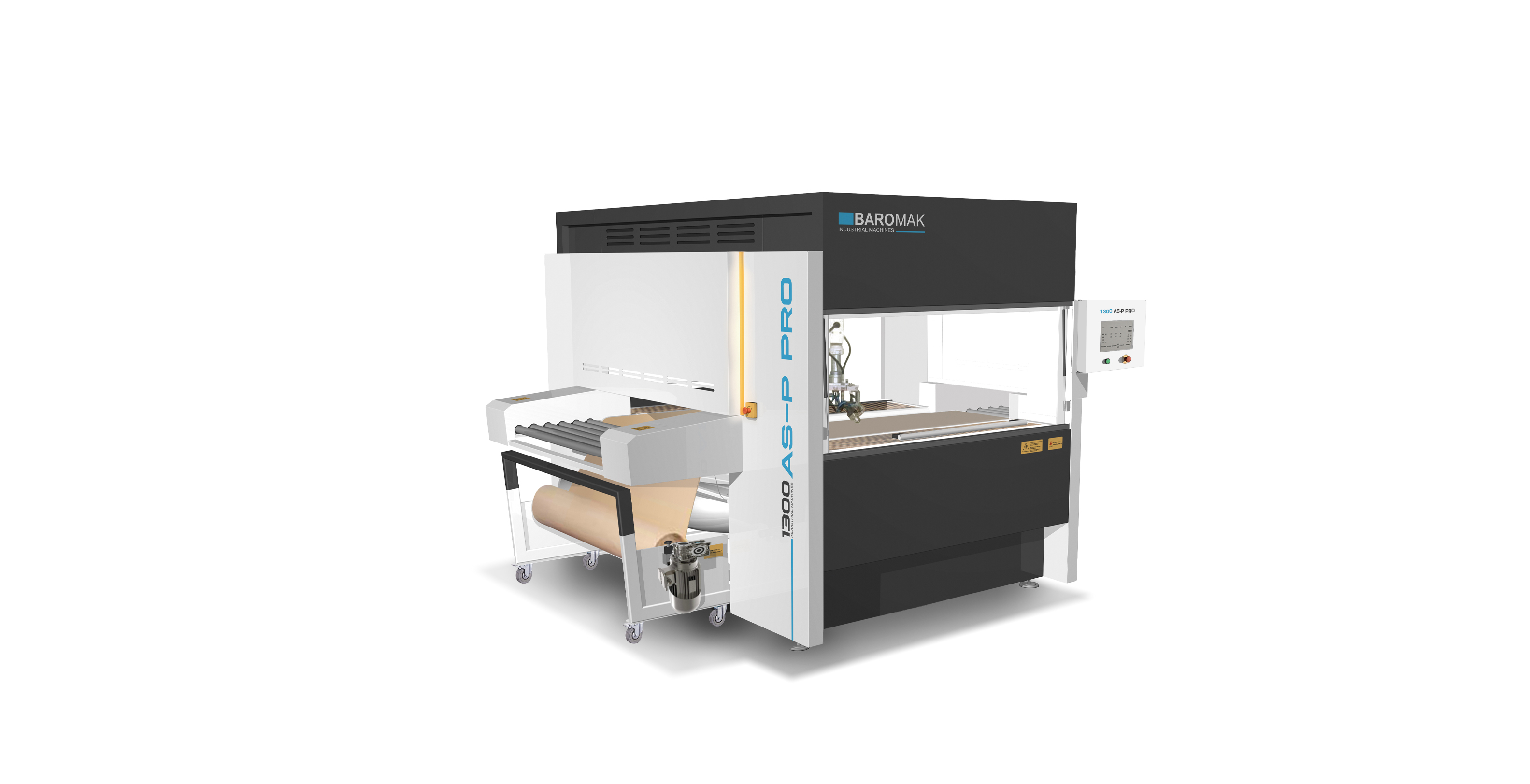
-Machine comes with 1 high-pressure pump and 4 high-pressure guns as standard. -Thanks to the reader sensors at the machine entrance, the product to be painted is automatically detected by the machine and the paint is applied only on the product. Thus, savings are achieved in the paint used. -Aspiration system, which plays an important role in balancing the cabin pressure and also evacuates the dirty air in the cabin, is offered as standard. -In the -1300 AS-P PRO automatic dyeing machine, the frequency-controlled ventilation system, which pumps clean air through F5 class filters into the system and whose flow rate can be adjusted, increases the dyeing quality. -All operating settings, as well as pump and gun pressures, can be easily controlled via the user-friendly interface via the 10-inch Industrial touch panel with IP68 protection standard.
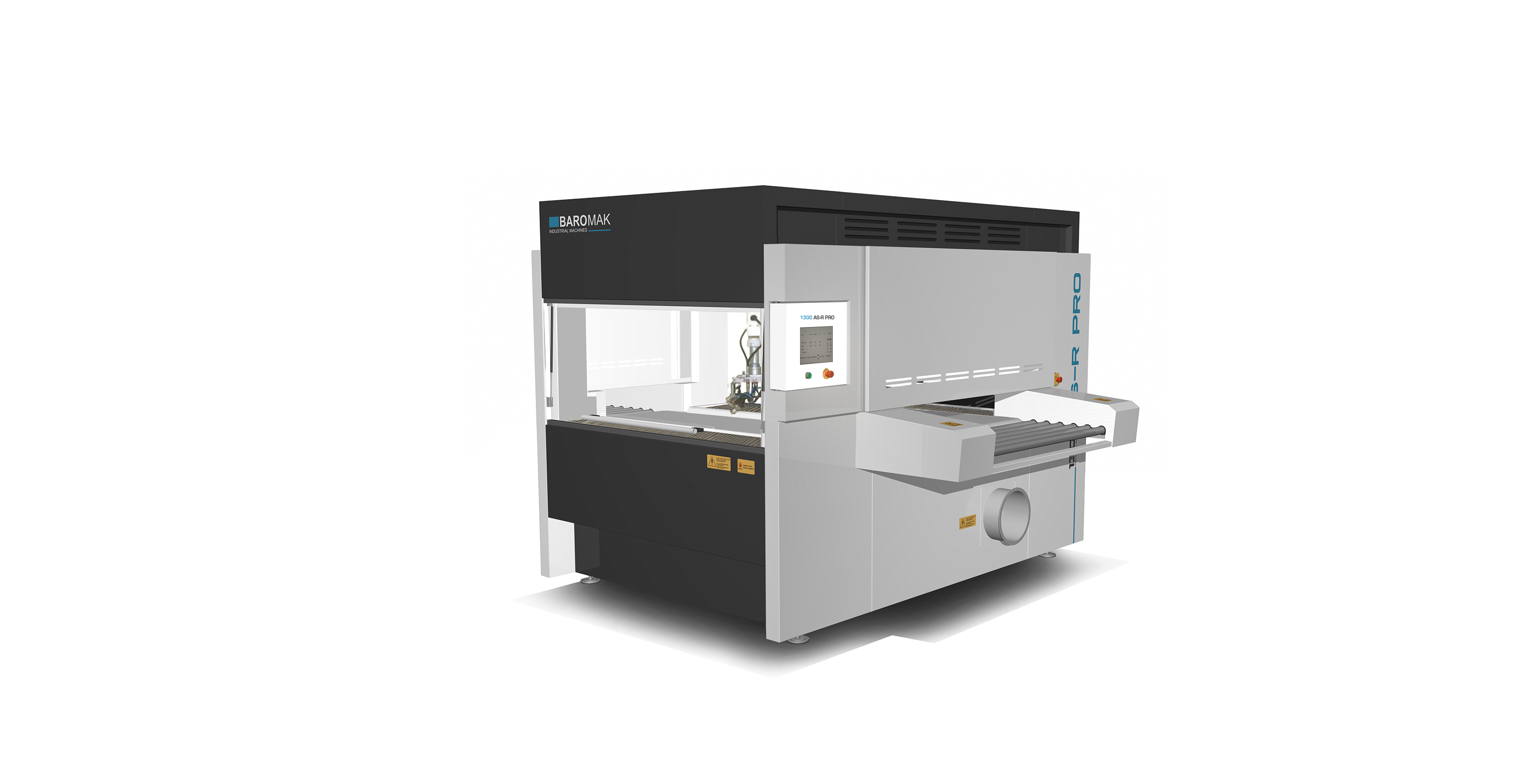
-The machine comes with 1 high-pressure pump and 4 high-pressure guns as standard. -Thanks to the reader sensors at the machine entrance, the product to be painted is automatically detected by the machine and the paint is applied only on the product. Thus, savings are achieved in the paint used. -Aspiration system, which plays an important role in balancing the cabin pressure and also evacuates the dirty air in the cabin, is offered as standard. Thanks to its paint stripping system, -1300 AS-R PRO constantly cleans the paint on the conveyor, ensuring that the conveyor remains dry and allowing the stripped paint to be reused. In the -1300 AS-R PRO automatic dyeing machine, the frequency-controlled ventilation system, which pumps clean air through F5 class filters into the system and whose flow rate can be adjusted, increases the dyeing quality. -All operating settings, as well as pump and gun pressures, can be easily controlled via the user-friendly interface via the 10 inch Industrial touch panel with IP68 protection standard.
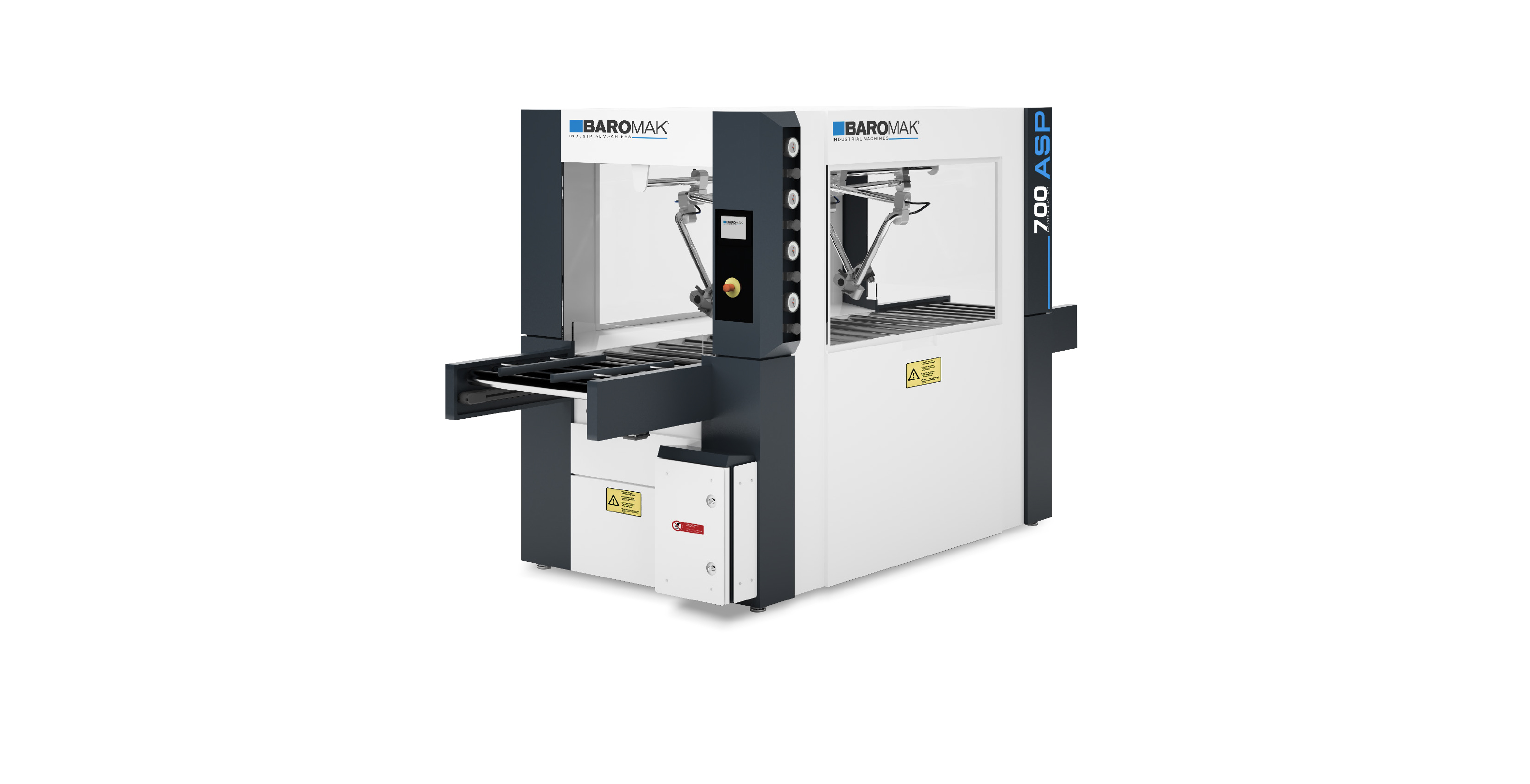
-Thanks to the adjustable part positioner plate system, products of different widths are adjusted and positioned before painting. -Thanks to the reader sensors at the machine entrance, the product to be painted is automatically detected by the machine and ensures that the paint is applied only to the product. In this way, the paint used is saved. -The machine comes with 1 low pressure pump and 4 low pressure guns as standard. -Aspiration system, which plays an important role in balancing the cabin pressure and also evacuates the dirty air in the cabin, is offered as standard. -Maximum performance in product dyeing quality is achieved thanks to the adjustable speed feature with the driven conveyor system. -With the help of remote connection, we can connect to your machine 24/7 and provide fault detection and training services.
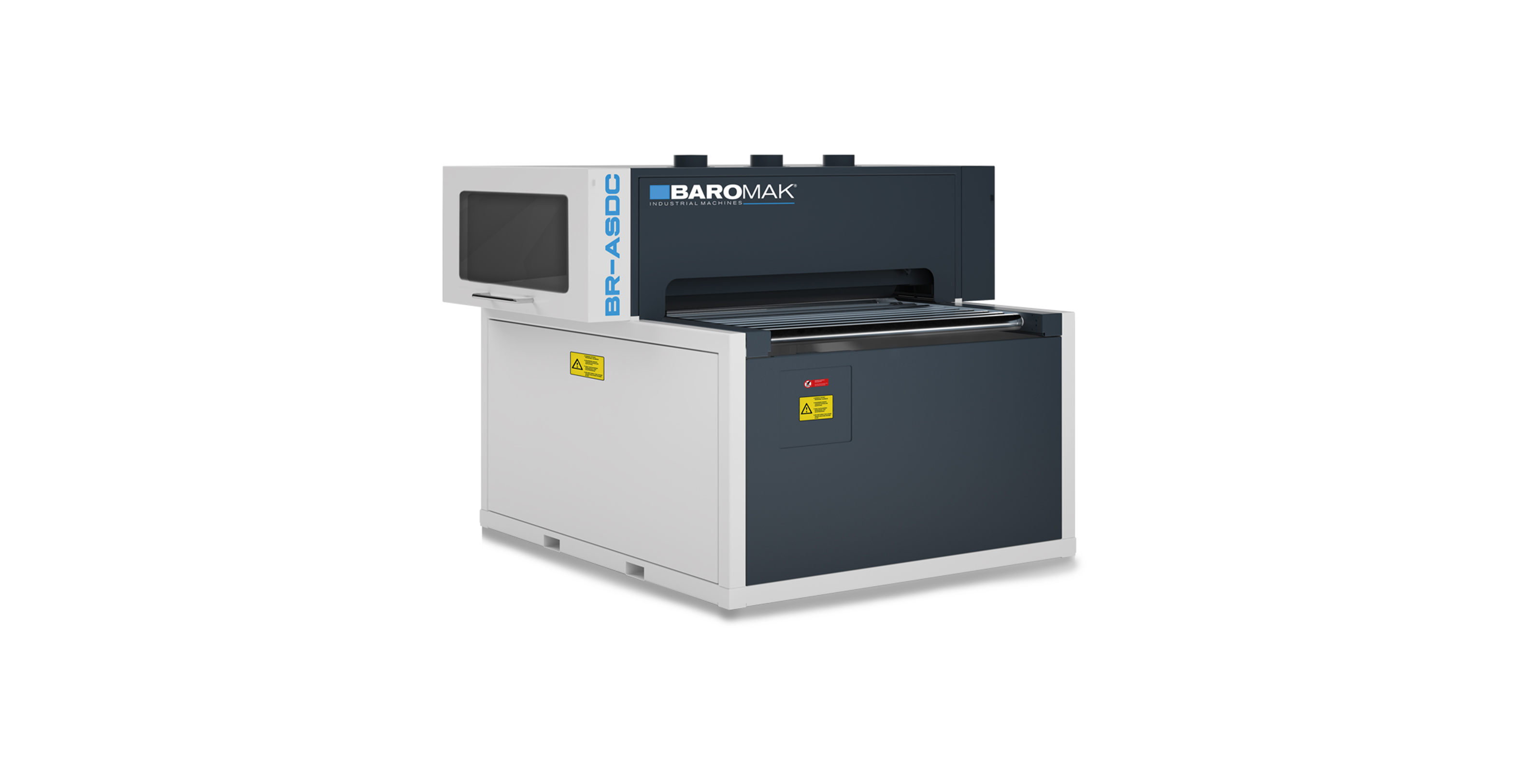
- Thanks to special brushes made of polyamide antistatic dust-free material with adjustable height, it cleans all dust particles that may remain on the product. - With the dust collection brush, all dust particles are completely expelled with the dust extraction unit. - With the antistatic bar feature, it eliminates static electricity on the product. The pre-painting antistatic bar system ensures better and higher-quality results on products free from static electricity, allowing the paint to adhere better to the surface. - The Anti- static Dusting Machine used before painting is integrated with the spreying machine and provides line usage, optimizing and minimizing production time.
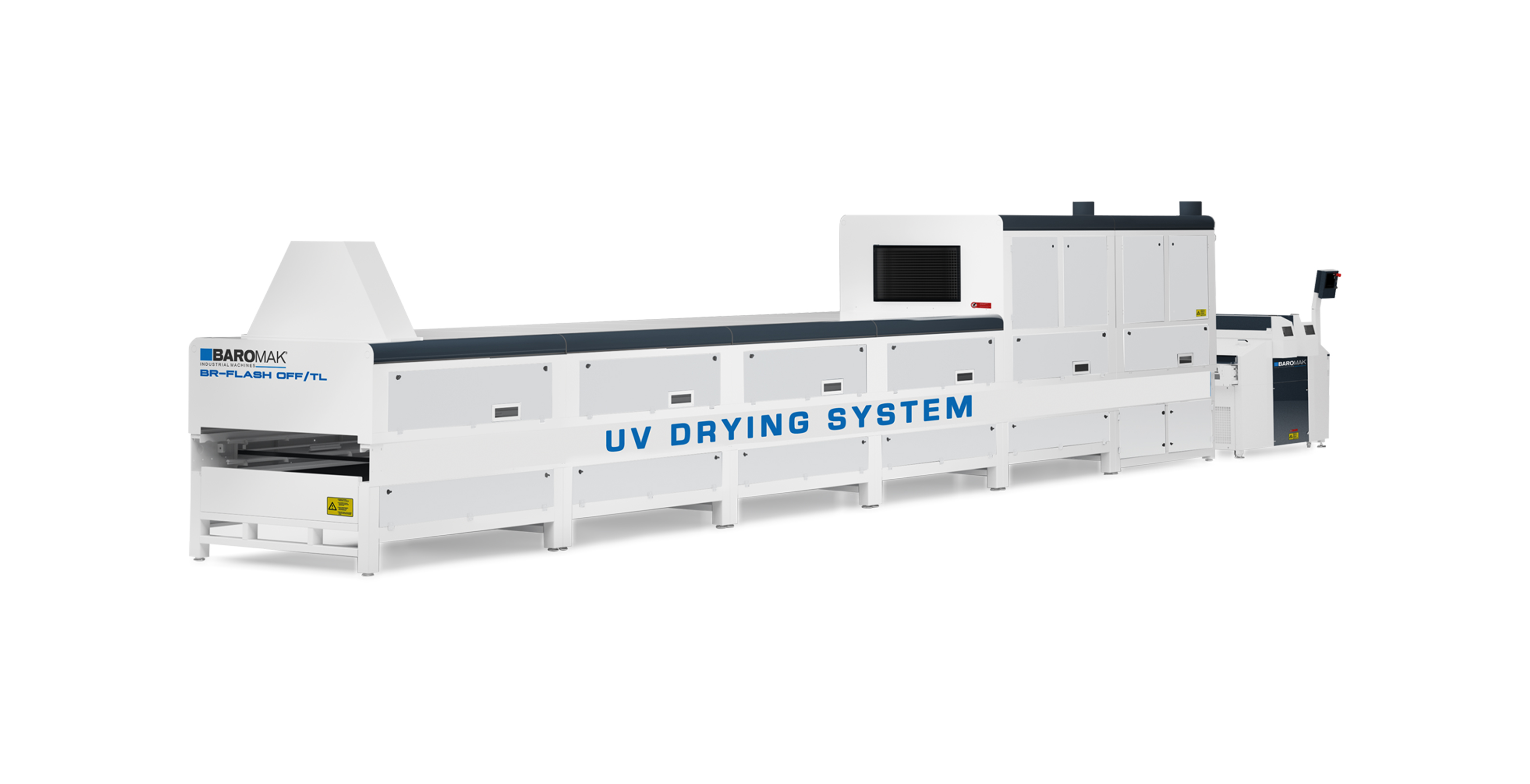
- Perfect performance for medium and large-scale serial operations. - The Hot Air Oven is used after the spray application machine, following the application of UV paint or varnish, to evaporate and remove the solvent in the paint and varnish before the UV gelation unit and UV final drying system. - Temperature-controlled and reverse-direction airflow circulation: The heat inside the tunnel and on the panels is electronically controlled to rise from cold to hot from entry to exit. Additionally, a uniform and layered airflow is provided in the opposite direction of the panel s travel direction. - Energy-saving modular body and ventilation: Closed-loop hot air circulation allows for air recovery. The modular body is thermally insulated, and the number of modules can be increased as needed to extend the tunnel. Air taken from the external environment is filtered before being introduced into the tunnel. - High-Quality MAT and GLOSS surfaces: Matte, glossy, and excellent surfaces are obtained with transparent varnish and pigmented UV paints. - Structure providing a dust-free environment: Designed to prevent dust entry into the modular tunnel for high-quality production. - Modular and insulated body: The furnace structure and air circulation are energy-recovered. The furnace body consists of steel structure and polyurethane accordion insulation in 2000 mm modules. Side panels are removable for maintenance and ease of use. The number of modules is adjusted according to the flash-off time, and our tunnel consists of 4 modules. - With the new generation inverter (electronic power supply) system, linear and stepless power adjustment is made in UV lamps, reaching the appropriate energy level linearly. At the same time, energy savings of up to 40% can be achieved. - The stainless steel roller conveyor ensures the smooth movement of panels to be dried under UV lamps. It is a furnace equipped with TL lamps used before the UV gelation unit, which provides final drying - curing after UV paint application in lacquer pouring or spray machines. - Panels are transported with 25 mm diameter chrome-plated rollers, resistant to heat. - The steel body is 12500 mm long and contains reflective insulation. - FU model UV curing systems are designed to dry UV chemicals applied to flat surfaces. The system operates with a new generation high-frequency electronic power supply and automatic material detection system, providing energy savings of up to 40%. Conveyor Features - The operating speed can be adjusted between 1 and 6 m/min with frequency control. - Panels are transported with 25 mm diameter chrome-plated rollers, resistant to heat. - The steel body is 12500 mm long and contains reflective insulation. - Gapless conveyor system allows the passage of small parts between conveyors and at entry-exit points. - Electrostatically painted machine surface provides protection against scratches and impacts. General Features - It allows the passage of materials such as MDF, ABS, DURALIT, PVC, GLASS, etc., with a thickness between 2 and 60 mm. - The body is specially designed for cold operation and easy intervention, with easily replaceable, highly reflective elliptical reflectors made of extruded aluminum. - Sliding cassette specially designed for quick troubleshooting, maintenance, and technical service intervention. - With the help of the new generation inverter (electronic power supply) system, linear and stepless power adjustment is made in UV lamps, reaching the appropriate energy level linearly. At the same time, energy savings of up to 40% can be achieved. - For each lamp, dynamic controlled fans are used for lamp cooling and exhaust gases, ensuring operational safety. During UV lamp power changes, the flow rates of the cooling fans change through frequency-controlled inverters, ensuring long lamp life. - The lamp life is precisely monitored using the lifetime counter on the touchscreen. - All functions can be monitored from the touchscreen using the ergonomic touch control panel. - The machine working height can be adjust
No represented companies found.
The company has no registered brand information.